Un bond en avant
Avec ses deux nouveaux modèles de camions souterrains articulés, les TH551 et TH663, Sandvik affine encore son approche polyvalente de la sécurité et de la productivité.
Les Sandvik TH551 et TH663 sont deux nouveaux camions souterrains offrant un cadre de travail exceptionnel aux opérateurs. Leur conception fiable optimise la disponibilité et le tonnage par heure.
Leur développement a commencé par un état des lieux. « Nous avons rendu visite aux compagnies minières et avons écouté ce qu’elles avaient à nous dire sur les camions et le transport », explique Minna Pirkkanen, chef de produit.
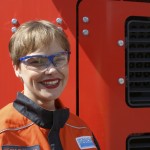
Minna Pirkkanen, chef de produit.
Ont résulté de cette enquête les TH551 et TH663, d’une charge utile de 51 et de 63 tonnes respectivement. Ils ont été conçus dans un souci d’interaction optimale avec les opérateurs, le personnel de maintenance, les chargeuses et les mines elles-mêmes.
« Le confort et le bien-être de l’opérateur sont très importants, reprend Minna Pirkkanen. Un opérateur heureux est généralement un opérateur plus productif. »
Tungstène à bord
Wolfram Bergbau und Hütten à Mittersill, en Autriche, a été l’une des premières entreprises à mettre en service les nouveaux modèles de camions Sandvik. L’exploitation minière souterraine a commencé en 1979. Aujourd’hui, un processus hautement automatisé permet d’extraire chaque année 500 000 tonnes de minerai de scheelite (CaWO4). La mine a opté pour un camion TH551 d’une charge utile de 51 tonnes.
« Il est très puissant et très productif, se félicite le responsable de l’exploitation Felix Gaul. Aujourd’hui, les mines doivent être de plus en plus productives. Ce sera le défi de demain, et pas uniquement pour notre mine. »
Et de détailler les fonctionnalités ergonomiques, lesquelles incluent une cabine sécurisée 35 % plus spacieuse que sur les modèles précédents, et équipée d’un harnais de sécurité quatre points et d’un fauteuil pour l’instructeur. Un écran de commande et de gestion indiquant toutes les informations vitales permet aux opérateurs de ne pas quitter la route des yeux. Le confort est assuré par un siège entièrement réglable et, autre innovation sur ces camions, une suspension avant. Le souci du détail va jusqu’à la présence d’une glacière dans le système de climatisation, laquelle permet à l’opérateur de stocker nourriture et boisson à bord. « Ce ne sont là que quelques exemples de l’ergonomie et de la convivialité de la cabine. C’est un lieu de travail vraiment très agréable. »
La sécurité a eu la priorité au cours du développement. Chaque modèle possède une soixantaine de fonctionnalités assurant la sécurité de l’opérateur, du personnel de maintenance et du camion lui-même, notamment des structures ROPS (sécurité anti-retournement) et FOPS (protection contre les chutes d’objets).
Du point de vue de la sécurité de la maintenance, l’entretien quotidien peut être effectué au niveau du sol pour limiter le risque de chutes. La conception permet également de remplacer les pièces de grandes dimensions, telles que la transmission, en immobilisant peu le véhicule.
Un problème en quête de solution a souvent été soulevé lors des dialogues avec les compagnies minières : les crevaisons. « La crevaison d’un des pneus d’un camion chargé en train de remonter une rampe d’accès est l’une des principales sources d’immobilisation et de danger, précise Minna Pirkkanen. On nous a dit que ça pouvait prendre jusqu’à trois jours pour réparer la roue et dégager la voie. »
Un tel incident bloquait complètement la production et la réparation exigeait une évaluation approfondie des risques afin d’éviter toute situation dangereuse. « C’est très difficile de soulever un équipement aussi lourd dans un espace confiné et pentu. »
10 arguments + 1 en faveur des TH
1. Chargeuses faisant pendant pour un chargement et un transport optimaux.
2. Haute capacité, haute vitesse et plus de disponibilité pour une productivité accrue.
3. Cabine ergonomique ROPS/FOPS avec siège pour l’instructeur.
4. Système intégré de commande et de gestion (VCM).
5. Système de contrôle de la production et de mesure du chargement.
6. Faible masse favorisant une faible consommation de carburant.
7. Points de maintenance quotidienne au niveau du sol.
8. Contrôle automatique de la pression des pneus en option.
9. Moteur conforme aux normes Tier4i/Étape IIIB en option.
10. Système de levage hydraulique embarqué en option pour plus de sécurité.
+ Suspension avant pour une conduite plus confortable.
Les camions TH551 et TH663 disposent, en option, d’un système de levage embarqué pour permettre un remplacement plus rapide et plus sûr des pneumatiques. Deux crics hydrauliques sont installés à l’avant, et deux à l’arrière. Tous sont indépendants les uns des autres.
Autre nouvelle fonctionnalité, le système de contrôle de pression qui vérifie la pression et la température interne des pneus en temps réel. Il permet d’identifier en amont les problèmes, notamment un feu potentiellement dévastateur prenant dans un pneu.
En ce qui concerne l’interaction des camions avec la mine et d’autres équipements miniers, le TH551 est le seul camion minier livré avec une option moteur Tier 4i/Étape IIIB, qui permet de réduire les gaz d’échappement et les besoins de ventilation qui en découlent. En ce qui concerne leur encombrement, les véhicules sont conçus pour des voies de transport de 5 x 5 et 6 x 6 mètres. Afin d’assurer la compatibilité des maillons de la chaîne de production, le volume des bennes est équivalent à trois godets des chargeuses Sandvik LH517 et H621 qui leur font pendant.
La principale difficulté a été d’accroître la charge utile, poursuit Minna Pirkkanen. En effet, les pneus imposent un certain plafond. Nous avons dû réduire la masse totale du véhicule. Nous avons mis au point un tout nouveau châssis en aciers haute résistance, ce qui nous a permis d’utiliser moins de matériau. »
La fabrication à partir d’aciers haute résistance est plus exigeante qu’avec des aciers traditionnels. Sandvik se repose sur sa grande expérience et son immense savoir-faire en matière de métallurgie pour tirer le meilleur parti des matériaux. Ainsi, le TH663 peut charger trois tonnes de plus que l’ancien modèle. Mais cela ne sert à rien si cette capacité supplémentaire n’est pas exploitée à fond. C’est pour cette raison que les deux camions disposent d’une série d’indicateurs lumineux situés sur leurs flancs. Ceux-ci indiquent à l’opérateur de la chargeuse si la benne est vide, presque pleine, pleine ou trop chargée. Ceci permet d’éviter tout mauvais usage du véhicule. « L’objectif est que chaque voyage soit productif. »
Les indicateurs lumineux ne sont qu’un des éléments du système intégré de contrôle de la production. C’est peut-être ce dernier qui améliore le plus la productivité : il estime le poids du chargement et associe cette information à d’autres portant sur la position et le quart de travail par exemple. L’opérateur peut également y enregistrer ce qu’il transporte, du minerai ou des morts-terrains. « Quand plusieurs opérations se déroulent en même temps dans la mine, on peut de ce fait retracer le chemin emprunté par chaque chargement. L’idée est de mesurer et d’optimiser l’activité », conclut Minna Pirkkanen.
Par: Åke R. Malm/Photos: Måns Berg