High yield and safety in the Andes
El Teniente, located in the Chilean Andes, is one of the largest underground copper mines on the planet. It is also one of the most complex, with many geotechnical challenges. By using automated solutions, the mine has significantly improved safety and productivity.
Now, together with Sandvik, state-owned company Codelco is creating the mine of the future.
In the next few years, the goal is for El Teniente to only have automated trucks and loaders.
Surrounded by sand-colored mountain peaks, El Teniente lies 2,100 meters above sea level and about 100 kilometers south of Santiago. The area is vast, and the car trip from the main gate to the mine’s opening takes more than an hour via winding roads.
El Teniente has a long history with the first copper ore being mined on an industrial scale in 1905. Since the early 1970s, the mine has been run by the state-owned mining company Codelco, and today, the company has over 3,800 employees with operations ongoing 24/7.
/https%3A%2F%2Fsolidground.sandvik%2Fwp-content%2Fuploads%2F2024%2F10%2Fcentro_rancagua_720.jpg)
Some of the operations in El Teniente are run from the nearby city of Rancagua.
“We are one of the largest underground mines in the world, producing 140,000 tons of extracted ore every day. El Teniente’s mining operations are massive, and we are using both block and panel caving processes,” says Rodrigo Andrades, Mine Manager.
How El Teniente’s geotechnical complexity breeds innovation
El Teniente consists of several operations located at different levels. Underground there is virtually an entire town with offices, maintenance workshops, warehouses and cafeterias for food services, among other things. The underground surface area is 385,000 m², and the countless mining passageways cover 4,500 kilometers throughout the mountain.
“This is one of the most complex mines in geotechnical terms worldwide. People from around the world come to us to see how we can utilize these immense complexities that we have,” says Rodrigo Andrades.
The geotechnical challenges in El Teniente have led Codelco to become an early adopter of innovative automation technologies. The company has long had a close partnership with Sandvik, and already in 2004, the first automation solution was implemented in El Teniente.
EL TENIENTE
El Teniente is located in the Libertador General Bernardo O’Higgins region in the Chilean Andes, about 100 km south of Santiago. The mine has been in operation since 1905.
The underground area is 385,000 m², and the mine has 4,500 kilometers of underground passages. The mine has over 3,800 employees and several contractors, with Sandvik being one of the largest.
Total production is 54,000,000 tons per year. Today, 35% is done using automated solutions, and the target is to reach 50-60% by 2025.
Today, AutoMine® technology is used in six different areas, and over 25 autonomous Sandvik loaders and trucks operate in the mine. This corresponds to approximately to about 35% of the mine’s total operations. And El Teniente’s automation journey is advancing at a fast pace, making significant strides towards its goals. New projects are underway, and by 2025 the goal is for 50-60% of the mine’s operations to be automated and digitized.
/https%3A%2F%2Fsolidground.sandvik%2Fwp-content%2Fuploads%2F2024%2F10%2FRodrigo--scaled.jpg)
“For us, the AutoMine® technology has two main objectives. The first is to improve safety and quality of life for our mine workers. The second objective is to incorporate more complex areas, for example sectors with mud water irrigation or with high seismic risks,” says Rodrigo Andrades.
The many benefits and possibilities of mining via remote control
A ten-minute drive from the mine’s ADIT-71 entrance, is Pacífico Superior, an area of the mine that has come the furthest with automation. Here production with Sandvik’s autonomous trucks and loaders is around 13,500 tons per day.
Operator Luis Rodrigo Merchant has just started his shift. From the control room, he and the other operators remotely monitor the four Toro™ LH621 loaders and four Toro™ TH663 trucks that tirelessly load and transport the ore some hundred meters away. While the trucks are fully automated and only monitored via the screens, there is one moment where, due to the changing nature of the muck pile, the loaders still need the assistance of a skilled operator like Luis Rodrigo Merchant: for bucket filling.
However, the difference from a fully manual equipment is huge. Seated in a comfortable operator’s chair, he uses a joystick to fill the bucket, far from the noisy and dusty environment that is typical in underground mining tunnels.
“I have been an operator for 17 years. Having driven manually for most of that time, I started working with Sandvik automation a few years ago. The difference to my quality of life is huge; the biggest advantages of automation for me are that I can do my job in an ergonomic chair and avoid the risks that noise and dust entail,” says Luis Rodrigo Merchant.
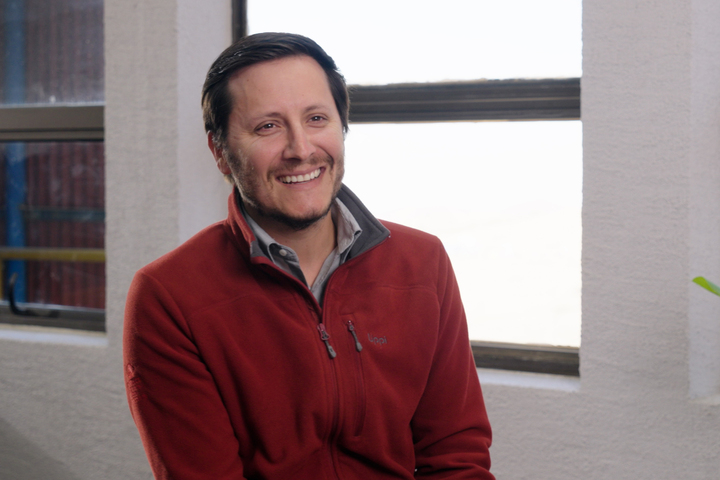
Francisco Castro is the Unit Head Diablo Regimiento Mine, a part of the mine that was considered inaccessible for many years. “Implementing Sandvik AutoMine® in Diablo Regimiento has helped us to prolong its production life and to have an extraction process that is both safe and efficient,” he says.
Right next to El Pacifico Superior is El Diablo Regimiento where Sandvik has three autonomous Toro™ LH517 loaders in operation. For many years, this part of the mine was closed off and considered inaccessible due to the high levels of humidity in the ore and the safety risks this brings. Now, Diablo Regimiento is producing an average of 23,000 tons a day.
“Implementing Sandvik AutoMine® in Diablo Regimiento has helped us to prolong its production life and to have an extraction process that is both safe and efficient. To date, we have recovered over a million tons of material that was previously captive there, given the high risks. Thanks to automation, the operators can manage the equipment safely without being exposed to pollutants and vibrations,” says Francisco Castro, Unit Head Diablo Regimiento Mine.
The future of mining
Sandvik is one of the largest providers of equipment, service, and digital solutions in El Teniente, and the company has skilled personnel on-site around the clock to offer lifecycle support solutions to seamlessly uphold Codelco’s day-to-day activities and ensure continuous operational efficiency. Additionally, Sandvik and Codelco have a very close strategic collaboration at all levels, and the autonomous solutions now being implemented in the mine are unique.
“Sandvik and Codelco have the same mining philosophy and have a strong focus on safety and reliability, increased production levels and reduced costs. We both believe that the key success factors for future mining are automation, digitalization, and electrification,” says Emilio Vega, Business Line Manager at Sandvik Mining and Rock Solutions. “Safety considerations include how people can be removed from hazardous environments as well as gaining more productivity by operating during shift change.”
CODELCO
Codelco stands for the Chilean National Copper Corporation. It is an independent company owned by the Chilean government and was founded in 1971.
Codelco’s core business is to explore, develop and extract mineral resources and to produce refined copper and by-products. The company has seven mining divisions and is one of the the world’s largest copper producers. In 2021, sales reached US$20 million. Its main market is Asia, followed by South America, North America and Europe.
Codelco’s headquarters is located in Santiago.
El Teniente is estimated to have a lifespan of up to 2050. Automation and digitization will be essential in order to continue mining copper further into the mountain and in areas with high safety risks.
The next step towards Codelco’s goal of operating the world’s most automated mine unfolded in 2023. Earlier this year, Codelco placed an order for an AutoMine® Core system and six autonomous Toro™ LH514 loaders to be deployed in its Recursos Norte operations.
The second phase of this contract, which covers 2024 through to 2027, includes seven additional Toro™ LH514s and an expansion for the AutoMine® Fleet system. After delivery, Codelco will have more than 40 autonomous Sandvik trucks and loaders in operation in El Teniente.
“Automation and electrification allows us to build the mine of the future. Sandvik is a strategic partner in this ongoing transformation, and our close and productive collaboration has brought us to where we are today. In a few years, our objective is to have a highly productive and safe mine with no manual equipment at all,” says Martín Galaz, Head of Automation Unit El Teniente Mine.
/https%3A%2F%2Fsolidground.sandvik%2Fwp-content%2Fuploads%2F2024%2F10%2Fmarti__n_galaz_720.jpg)
El Teniente is estimated to have a lifespan up to 2050. Automation and digitization will be essential in order to continue mining copper further into the mountain and in areas with high safety risks. “Automation and electrification allow us to build the mine of the future,” says Martín Galaz, Head of Automation Unit El Teniente Mine.
SANDVIK AUTOMATION SOLUTIONS IN EL TENIENTE
Sandvik has a long-standing relationship as a strategic supplier of automation technologies and support services to Codelco.
To date, Sandvik has implemented over 25 automated loaders and trucks and six AutoMine® projects in El Teniente. Six projects use the AutoMine Core system and several future AutoMine® Core projects are underway.
AutoMine® Fleet is a comprehensive automation platform for fully autonomous operations tailored to mass mining operations. It brings together industry-leading digital solutions for stable underground connectivity, powerful data collection and analysis, an advanced fleet of automated equipment options inclusive of mass mining production monitoring, and Lifecycle Support Solutions to make underground mining safer, more sustainable and productive.
AutoMine® Multi-Lite is an automation system, which enables each system operator to remotely control and simultaneously supervise multiple automated Sandvik underground loaders and trucks. With AutoMine® Multi-Lite each piece of equipment completes automated missions within its own dedicated production area.
Toro™ loaders and trucks seamlessly integrate the AutoMine® system to the equipment control system, providing improved safety, productivity and efficiency for underground mines.