Grandes avanços
Com os novos modelos de caminhões subterrâneos articulados TH551 e TH663, a Sandvik eleva a segurança e a produti-vidade a um novo patamar.
Sandvik TH551 e TH663 são dois novos caminhões subterrâneos com ambiente de operação de primeira classe. Um projeto confiável maximiza os tempos de disponibilidade e de toneladas por hora. O primeiro passo no desenvolvimento foi uma pesquisa real.
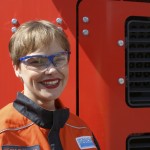
Minna Pirkkanen, gerente de produto.
“Fomos até as mineradoras e ouvimos seus problemas referentes a uso e elevação de caminhões”, lembra a gerente de produto Minna Pirkkanen.
Tungstênio a bordo
Uma das primeiras empresas a colocar um dos novos modelos de caminhões da Sandvik em ação foi a Wolfram Bergbau und Hütten AG em Mittersill, Áustria. Lá, a mineração subterrânea começou em 1979 e, atualmente, 500 mil toneladas de minério de Scheelita (CaWO4) são extraídas por ano em um processo altamente automatizado. A mina optou por um TH551 com capacidade de carga de 51 toneladas.
“É muito poderoso e produtivo”, diz o gerente de mineração Felix Gaul. “Hoje em dia, todas as minas têm que ser cada vez mais produtivas. Esta será a luta do futuro, não só para nossa mina.”
O resultado foram os TH551 e TH663, com cargas de 51 e 63 toneladas, respectivamente. Eles foram projetados para ótima interação com os operadores, equipe de manutenção, carregadeiras e com a própria mina. Vamos analisar estes pontos.
“O conforto e o bem-estar do operador são muito importantes”, diz Pirkkanen. “Um operador feliz é geralmente mais produtivo.”
Pirkkanen fala sobre as características ergonômicas, que inclui uma cabine de segurança 35% maior que nos modelos anteriores e equipada com cinto de segurança de quatro pontos e assento extra. Um display de controle e gerenciamento do veículo com todas as informações vitais permite que os operadores mantenham seus olhos na estrada. O conforto é proporcionado por um assento totalmente ajustável e, outra novidade, suspensão dianteira. A atenção aos detalhes inclui uma caixa de refrigeração integrada ao sistema de controle de temperatura. Isso permite que o operador mantenha comidas e bebidas resfriadas a bordo.
“Estes são apenas alguns exemplos de ergonomia e facilidades da cabine”, conta Pirkkanen. “É muito agradável.”
A segurança foi o foco principal durante o desenvolvimento dos modelos TH551 e TH663. Cada um tem mais de 60 recursos de segurança para proteger o operador, a equipe de manutenção e o próprio caminhão. Isso inclui cabine certificada com estruturas de proteção de capotagem e contra queda de objetos (ROPS e FOPS, em inglês).
Ao olhar a segurança da perspectiva de manutenção, serviços diários podem ser feitos do chão para reduzir o risco de queda. O projeto também permite a substituição de grandes componentes, como a transmissão do motor, com um tempo mínimo de inatividade. Uma área específica de melhoria que surgiu no diálogo com as mineradoras foi punção.
11 benefícios dos caminhões
1. LHDs correspondentes para carregamentos e transportes otimizados
2. Alta capacidade, velocidade e disponibilidade para maior produtividade
3. Cabine do operador ergonômica, com segurança ROPS/FOPS e assento extra
4. Sistema integrado de Controle e Gerenciamento do Veículo (VCM, em inglês)
5. Sistema integrado de medição de peso e monitoramento de produção
6. Peso baixo, resultando em baixo consumo de combustível
7. Pontos de manutenção diária acessíveis do solo
8. Sistema opcional de monitoramento dos pneus
9. Motor correspondente ao Tier4i/Stage IIB opcional
10. Sistema de macaco hidráulico interno para aumentar a segurança
+ Suspensão dianteira para condução mais suave
Uma situação que gera inatividade e perigo acontece quando o pneu do caminhão fura enquanto ele sobe totalmente carregado uma rampa”, conta Pirkkanen. “Fomos informados de que pode levar até três dias para consertar e mover o veículo.”
Isso pararia a produção por completo, e consertar o pneu exigiria uma avaliação de risco minuciosa para evitar situações perigosas.
“É muito difícil suspender um equipamento tão pesado em um espaço confinado e inclinado”, diz Pirkkanen.
A solução que o TH551 e o TH663 oferecem é um sistema de elevação interno opcional para trocar o pneu de maneira mais rápida e segura. São dois macacos hidráulicos na frente e dois na traseira, trabalhando independentemente um do outro. Outra novidade é um sistema de monitoramento dos pneus que registra a pressão e a temperatura interior em tempo real. Isso torna possível identificar problemas antes que eles ocorram.
Então chegamos à interação dos caminhões com a mina e outros equipamentos de mineração. Para reduzir as emissões do escapamento e os requisitos de ventilação correspondentes, o TH551 é o único caminhão subterrâneo disponível com um motor alternativo compatível com o Tier 4i/Euro Stage IIIB. Em relação à carga, eles são feitos para transporte de 5m2 e 6m2. Para certificar que os elos da cadeia de produção combinem entre si, as caçambas acomodam precisamente três passagens das carregadeiras correspondentes Sandvik LH517 e LH621.
Omaior desafio que tivemos foi aumentar a capacidade de carga, considerando os limites dos pneus”, lembra Pirkkanen. “Então tivemos que reduzir o peso total do veículo. Desenvolvemos uma estrutura completamente nova, com aços de alta resistência, que exigiu menor quantidade de material.”
Trabalhar com aços de alta resistência exige mais do que com os tradicionais. A Sandvik conta com ampla experiência e know-how metalúrgico para tirar o máximo proveito dos materiais. No TH663, o resultado são três toneladas a mais na parte de trás, comparado com o modelo anterior. Mas isso não ajuda se a capacidade extra não for totalmente utilizada. Por isso, os dois caminhões têm um conjunto de lâmpadas indicadoras de peso no exterior. Elas avisam ao operador da carregadeira quando a caçamba está vazia, cheia ou sobrecarregada. Isso também protege os caminhões da utilização indevida.
“O objetivo é garantir que toda viagem seja produtiva”, diz Pirkkanen.
Os sinais são apenas parte de um sistema de monitoramento integrado de produção. Este é, talvez, o recurso de melhoria de produtividade mais significativo. Ele sente o peso na caçamba e combina isso com informações sobre posição e deslocamento, por exemplo. Além disso, o operador pode registrar no sistema o que está a bordo do caminhão, minério ou sobrecarga.
“Quando se tem muitas operações diferentes acontecendo na mina, você é capaz de rastrear a rota de cada carga”, diz Pirkkanen. “A ideia é medir e otimizar a operação.”
Texto: Åke R. Malm/Foto: Måns Berg