The mining factory
PARKES, Australia. Rio Tinto/Northparkes Mines in central New South Wales, Australia, has successfully implemented Sandvik Mining’s AutoMine loading system over the past three years – and is now moving towards 100 percent autonomous loading.
What is automine loading?
AutoMine loading allows remote operation and supervision of an automated underground loader or truck fleet from a surface control room. The autonomous fleet is operated in an area that is isolated from personnel and other equipment, greatly enhancing underground mine safety. Driving (tramming) and dumping are fully automated, while bucket loading is performed using tele-remote operation. A single system operator is able to manage the operation of multiple automated machines. A wide range of Sandvik underground loaders and trucks can be fitted with the AutoMine onboard package.
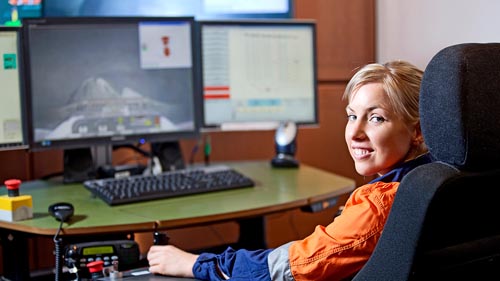
Autonomous ore loading
At Northparkes, AutoMine is currently operating at the mine’s E48 block cave, consisting of 10 extraction drives with a total of 214 draw points. Six Sandvik LHDs — five LH514Es and one LH514 — have been fitted with the AutoMine system, which allows for safe operation autonomously from the surface control room. The surface operator is only required to operate the loader for a short time in each cycle: simply filling the bucket at the draw point. The loader then trams autonomously with a full bucket to the ROM bin, dumps and returns to the next designated draw point. Currently the AutoMine system is working on 40 percent of Northparkes’ underground operations, a figure that will soon increase to 80 percent. For the rest of the mine’s extraction drives, autonomous operation is planned to start in early 2013.