Intelligent designs
Sandvik Mining has launched Sandvik DD422i, the first of its Next Generation underground hard rock drill rigs, with a strong emphasis on the human-machine interface. The completely redesigned drill offers top-level performance in safety and ergonomics for operators, increased productivity at a lower cost and wide-ranging automation options to carry the mining operation far into the future.
Development drilling is the key to unlocking an underground mine’s ore, and the new Sandvik DD422i drill rig offers a wide range of new features to improve excavation of these tunnels in hard rock mines.
Trendsetter
Sandvik DD422i is the first release in the company’s upcoming generation of advanced underground drill rigs. These Next Generation jumbos respond to future trends in mining: operators must comply with increasingly challenging safety and environmental requirements, while mine managers need more efficient cost control and must be able to provide new operators with advanced on-board drilling assistance in typically remote mining locations.
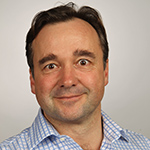
Alain Comorge, Sandvik product line manager, face drills, bolters and low profile underground drills.
“These super-trends were the main drivers for our Next Generation drill programme,” says Alain Comorge, Sandvik product line manager, face drills, bolters and low profile underground drills. “We want to be there for our customers and, as an original equipment manufacturer, to help them face these challenges.”
Four key elements make Sandvik DD422i a unique new rig that will raise the industry standard to a new level: a new drilling and boom control system, better cabin ergonomics, an improved carrier, and wide-ranging drilling assistance and automation options.
Better speed and service life
The rig’s drilling and boom control system for the first time introduces torque-based drilling control in the Sandvik mining jumbo fleet. According to test results, the optimized torque control significantly reduces jamming of the drilling tools and helps operators not only to gain better service life for their tools but also to reduce the throughput time in face drilling. The improved control system also helps to increase the speed and accuracy of the boom movements.
Tech specs
Power pack: 2 x 75 kW IE3
Diesel engine: Cummins QSB4.5, 119 kW, Tier 3 (optionally Tier 4 F)
Transmission: Hydrostatic
Cabin: FOPS and ROPS
Drilling coverage: 10,270 x 6,590 mm
Hole diameter: 43–63 mm
Hole length: Max. 5,270 mm
Rock drill: Sandvik RD525
Height: 3,145 mm
Width: 2,310 mm
Turning radius: 7,000 mm (out), 4,050 mm (in) with 12’ feed
Operating weight: 26 tonnes
Control system: Sandvik Intelligent Control Architecture (SICA)
Automation levels: Silver/Gold/Platinum
Another key feature of Sandvik DD422i is the modern ergonomic cabin. The entirely new design improves visibility during both drilling and tramming, thanks to lower and wider boom support and larger windows. The windows and the steel structures of the cabin frame include special acoustic materials that significantly reduce noise levels. Dust levels have also been optimized through careful design and comprehensive simulations. All the controls for drilling and tramming are ergonomically located and freely adjustable by operators according to personal preferences.
“The entire cabin is more open and spacious, and we truly believe that this is the most comfortable underground working environment in the whole industry,” Comorge says.
Carrier evolution
The third major feature of Sandvik DD422i is the improved carrier based on the latest available technology.
These new solutions include a Tier 4 F engine option for reduced emissions, hydrostatic transmission for better tramming control as well as comprehensive diagnostics, service points accessible at ground level, and light yet durable covers to make the maintenance as easy as possible. The multi-voltage electric system is a novelty that allows relocation of the drill rig from one electrical system to another with minimal changes. A special current reducer unit is an option that can decrease the current draw by up to 20 percent.
Multi-level package
In addition, Sandvik DD422i offers an exceptionally wide range of drilling assistance and automation levels to improve productivity and lower costs as well as reduce the training load. The Silver level features the basic measurements of rock drilling, including drilling depth and feed angle. The Gold level has additional capabilities for on-board visualization of the drill plan as well as the market-leading iSure planning, reporting and optimization software. The Platinum level maximizes the automatic face drilling capabilities of the rig.
Platinum, the highest automation level, also includes a new, semiautomatic feature combining both manual and automatic drilling functions. “Based on feedback from our tests, customers truly love this feature as it’s specially designed to more efficiently interlink these two ways of operating the rig,” Comorge says. “We already had a strong and reliable drill rig to begin with. Now the advanced automation adds a brain to it.”
The project progressed smoothly, and the first prototype drill rig was unveiled in front of customers in September 2013. From the very beginning, the goal was to build a drill rig that could help mining companies respond to requirements emerging in both the medium and long term. “Our new Sandvik DD422i development jumbo provides a clear direction to the future of mining, incorporating a host of new features for more efficient drilling,” Comorge says.
Smart drilling for future mines
Sandvik DD422i boasts powerful automation capabilities for the planning, measuring and follow-up of drilling operations based on the Sandvik Intelligent Control Architecture (SICA), which provides commonality with other Sandvik equipment.
The rig is compliant with teleremote control and can be integrated with the AutoMine Drilling system for autonomous drilling operations and thus reduced risk to personnel, better accuracy and higher productivity.
AutoMine Monitoring offers real-time data collection for efficient fleet management and predictive maintenance, while AutoMine Process Management keeps shift supervisors up to date on rig availability, utilization, condition and output and enables optimization of the mining operations. Furthermore, the Iredes v1.0 interface provides compatibility with third-party mine planning systems.
Text: Turka Kuulmala Photo: Måns Berg