Raising awareness
Orefields,a newly formed raise boring contractor inside the Arctic Circle in northern Sweden, is building on its backyard success while sustaining a steadfast commitment to safety.
Håkan Antonsson exudes an enthusiasm that can’t be faked as he highlights the features of his 22-tonne raise borer in a workshop 775 metres below Kirunavaara mountain at LKAB’s famed Kiruna mine in Sweden.
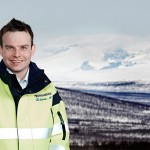
Håkan Antonsson founded Orefields in 2010.
Antonsson, an entrepreneur with a background in electrical engineering, had never operated mining machinery of any kind before he founded Orefields in 2010.
“I was performing electrical maintenance on raise borers and became fascinated with them,” he says. “I wanted to work with the machines in a different way, and I just had a feeling I could do it better and safer than other companies.”
Three years later, Orefields is assembling an impressive resume that includes multiple successes at the world’s largest underground iron ore operation, widely considered the world’s most modern underground mine.
“We’re thinking in a different way, and we’re very glad that LKAB has bought into our philosophy,” says Anders Jonsson, Orefields’ senior supervisor and mechanical superintendent, whose 15 years of raise boring experience span four continents. “Our goal is not to be the biggest raise boring company in the world. Our goal is to have high performance and a high safety standard.”
A safer alternative
Raise boring is a safer alternative to the conventional drill and blast method. Once the reamer head is attached to the borer, no personnel need to be in a shaft until spoil removal, eliminating exposure to falling rocks and explosives. Raise boring also disturbs the rock structure less than blasting, so the method can be used safely in geologically sensitive mines.
Raise boring was developed to meet underground mining demands, but new applications continue to arise due to its inherent safety benefits and other advantages over conventional drilling and blasting.
The raise boring method enables construction of circular mechanized shafts between two mine levels without the use of explosives. A borer is set up on the upper level and drills a narrow pilot hole, typically between 23 and 35 centimetres, to accommodate a drill string. A reamer head is then attached to the drill from the lower level and raised back towards the machine.
“Raise boring holes have very smooth walls compared to blasted holes, and you rarely need to reinforce them with rock bolts or other ground support,” Jonsson says. “You can also raise bore in areas where you couldn’t drill and blast.”
Not only is raise boring safer than conventional methods, it’s also quicker and more economical because it works in a non-cyclic fashion, which facilitates faster advance rates, and because it requires less manpower while leaving less rock behind.
Raise boring can be used for a variety of mining applications, from ore shafts – where ore is tipped directly into crushers – to shafts for ventilation, water or cable installations.
“It’s becoming more and more popular,” Jonsson says. “There are no real disadvantages with it.”
Almost two years after Antonsson founded the company, and after he and Jonsson had spent many months amassing equipment as small as screwdrivers and as big as the borer itself, Orefields started operations on LKAB’s Block 19 in January 2012.
The company bored four inclined ore production shafts about 50 metres long and 2.4 metres wide. LKAB’s Mikael Hjortborg oversaw the four-month project.
“Orefields finished the project on time and with very high safety standards,” Hjortborg says. “We preach ‘safety first’ here at LKAB – we’re always striving to eliminate accidents – and Orefields shares that vision.”
Whether it’s careful consideration and analysis of the risks and benefits of moving its massive boring machine or cautious handling of the 1.5-metre drill rods that weigh nearly 500 kilograms each, the Orefields team never loses sight of the importance of safety.
“It’s possible to always work safely underground,” Antonsson says. “That’s our philosophy. Safety is everything in this business.”
Orefields operates a TRB Rhino 1298 DC raise bore for its shaft drilling projects. The company also uses Sandvik Mining equipment for all boring, from stems and cutters to high-penetration reamer heads that are quick to assemble and highly stable and that boast low torque and maintenance demands.
Big power
Orefields, a new raise boring contractor based in northern Sweden, operates a TRB Rhino 1298 DC raise borer from TRB Raise Borers OY (CEO Jarko Salo) for its shaft drilling projects. The versatile machine is nearly five and a half metres tall, weighs 22 tonnes with crawler, and packs plenty of power in its mid-sized frame for holes 2.4 to 3.5 metres in diameter.
“When you’re building up a company, it’s very important to not only have a good team surrounding you, but also good suppliers,” Antonsson says. “We have a great partnership with Sandvik.”
Jonsson adds: “I’ve been working with both Sandvik and other leading raise boring suppliers for many years, and Sandvik is my favourite by far. They build very reliable equipment and they deliver fast. If we ever have a problem with something, we just call Göran Strand, their raise boring product line manager, and he solves it. We have great communication and a great relationship, and we appreciate having a partner that shares our safety focus.”
Sandvik reaming heads and cutters are engineered for optimum service life in any rock condition. Strand says the ultimate goal, which is already achieved in many projects, is to enable operators to finish a raise in one pass without ever having to lower the reaming head for service.
“Performing service under or near an open raise can put operators in a vulnerable position, because they can be exposed to falling rocks from the face where the reaming was stopped,” Strand says. “Extended cutter life reduces the need for service, in turn making the equipment much safer to use.”
Orefields built a custom operator cabin that features more amenities than many studio apartments. “I can live there for a month at a time,” Antonsson jokes.
The outside of the cabin is fixed with emergency LED lights that activate during any power failure underground. Orefields stores tools and spare parts in a custom shed, and the company emphasizes order and neatness wherever it bores.
“A tidy worksite is a safer worksite, and a more productive one too.”
Orefields has an emergency box for oil spills caused by hydraulic accidents. “But we never grab anything out of the emergency box unless there’s an emergency.”
Another safety initiative that has impressed many mineworkers at LKAB is a lighted, portable “assembly point” sign the Orefields team erects near each worksite.
“We’re always trying to do our best to think in innovative ways. We should be a company always looking into the future.”
A few months after its debut project, Orefields took on a project in Shaft 91 at the Kiruna mine, drilling a single three-metre-wide, 130-metre-long inclined shaft to replace a collapsed ore pass. The company has since completed a multiple-shaft assignment for Swedish engineering company NCC in the Kiruna mine.
In addition to its safety commitment, Orefields also prides itself on precision, averaging less than 1 percent deviation.
Orefields hopes to take its operation global, and the company has started by developing a positive domestic reputation.
“From the beginning, LKAB took a chance signing a contract with a company that at that point didn’t even have a machine,” Antonsson says. “It’s made the success that much sweeter for everybody. We’re so fortunate to have had these opportunities to prove that a small company with the right people can also do these complex raise boring jobs. Our goal has been first and foremost to establish ourselves here locally, and we feel we’re well on our way. We are only starting our journey along this road.”